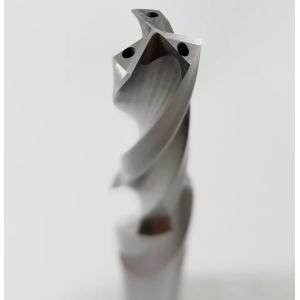
Add to Cart
Carbide drills are widely used in CNC (Computer Numerical Control) machining due to their excellent cutting performance, durability, and heat resistance. When selecting a carbide drill for CNC machining, several factors should be considered:
Drill Geometry: Carbide drills come in various geometries, such as twist drills, center drills, spotting drills, and more. The drill geometry should be chosen based on the specific machining operation and the desired hole characteristics.
Point Angle: The point angle of the carbide drill refers to the angle between the drill's cutting edge and the centerline of the drill. Common point angles range from 118 degrees to 140 degrees. Lower point angles are generally used for softer materials, while higher point angles are suitable for harder materials.
Flute Design: The flute design of the carbide drill affects chip evacuation and cutting efficiency. Common flute designs include straight flutes, helical flutes, and parabolic flutes. Helical or parabolic flute designs are often preferred for CNC machining due to their improved chip evacuation capabilities.
Coating: Carbide drills are often coated with various materials to enhance their performance. Common coatings include TiN (titanium nitride), TiCN (titanium carbonitride), TiAlN (titanium aluminum nitride), and AlTiN (aluminum titanium nitride). Coatings can provide benefits such as increased hardness, improved lubricity, reduced friction, and extended tool life.
Diameter and Length: The diameter and length of the carbide drill should be selected based on the desired hole size and the thickness of the material being drilled. It's important to ensure that the drill's length is suitable for the CNC machine's capabilities and the depth requirements of the hole.
Cutting Parameters: The cutting parameters, including cutting speed, feed rate, and depth of cut, should be optimized for the specific material being drilled, the drill geometry, and the CNC machine's capabilities. Proper cutting parameters help maximize the drill's performance and tool life.
Carbide drills are widely used in various machining applications requiring high-performance drilling. Here are some of the common applications of this type of drills:
Carbide drills are widely employed in metalworking industries for making holes in a broad scope of metals, such as steel, stainless steel, cast iron, aluminum, and alloys. Such drills are used in fields such as automotive parts producing, aerospace components making, general metal fabrication, tool and die making, and precision machining.
Carbide drills play a crucial role in the automotive industry, due to their importance in the production of components such as engine blocks, crankshafts, cylinder heads, connecting rods, and transmission parts. Thanks to the accuracy of these drills, it is possible to make reliable and efficient automotive parts.
Carbide drills are perfect for the aerospace industry, which puts a high value on precision and quality. As such, carbide drills are used for creating holes in elements such as aircraft structures, engine components, turbine blades, landing gear, and other essential aerospace parts. Their accuracy helps in meeting the tight tolerances and perfect surface finishes required for these components.
Carbide drills also find applications in the oil and gas field, mainly in order to make holes on the components involved in explore, extraction, and refining processes. In addition to the high-performance of these drills, they are also capable of handling drilling operations in challenging materials and conditions.
Carbide drills are increasingly employed in the medical field, due to their high accuracy and precision. In particular, these drills are used for creating holes in medical devices, implants, and surgical instruments, taking into consideration that the successful implementation of implants and medical procedures depends on the precision of these holes.
In the electronics industry, carbide drills are needed to create holes in printed circuit boards (PCBs) and electronic components. Such drills provide great precision and accuracy for making holes of various sizes, making the assembly of electronic circuits possible.
Carbide drills have made their way into woodworking activities, mainly because they are suitable for drilling holes in wood, plywood, and other wood-based materials. Moreover, these drills are specially designed to provide long-term performance and excellent results on hardwoods and composite woods.
Additionally, carbide drills are essential tools for machining tasks, repair and maintenance operations, fabrication, mold making, and tool and die production. They can be used to make holes on a range of materials, including ferrous and non-ferrous metals, plastics, composites, and many more.
We provide high-quality Tungsten Carbide Drill Bits with the following attributes:
Technical Support and Service for Tungsten Carbide Drill Bits
Tungsten Carbide Drill Bits are securely packaged in cardboard boxes or plastic containers. Each box or container contains 10 drill bits.
We use reliable shipping partners to ensure that your order arrives safely and quickly.
```